Progressive cavity pumps are widely used in various industries for their efficiency in handling viscous fluids. One of the primary applications of these pumps is dosing, where precise amounts of fluid are delivered to a process. This article explores the key aspects of dosing with progressive cavity pumps, including their advantages, working principles, and considerations for effective dosing.
What is a Progressive Cavity Pump?
A progressive cavity pump consists of a helical rotor and a stator. The rotor turns within the stator, creating cavities that trap and move the fluid from the inlet to the outlet. This mechanism allows for a continuous flow, making it ideal for dosing applications where consistent delivery of fluids is crucial.
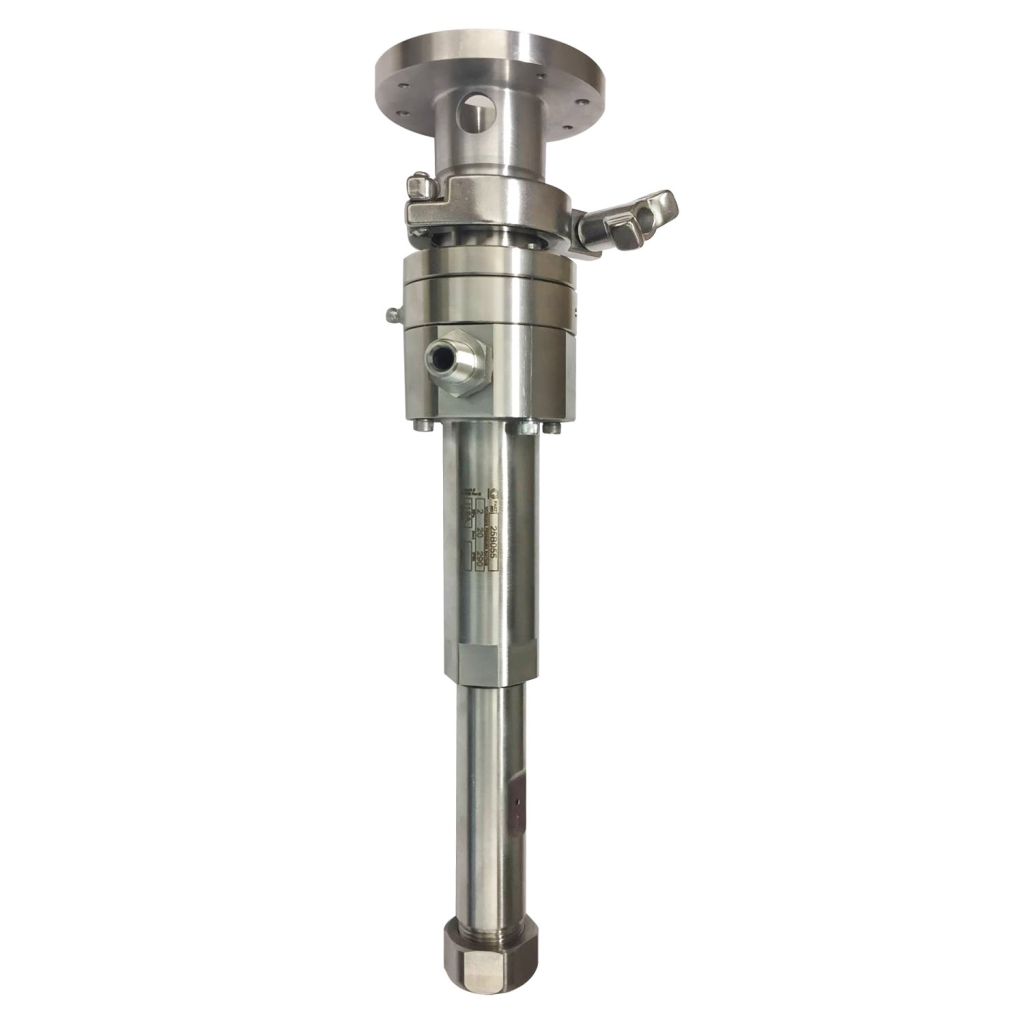
Advantages of Dosing with Progressive Cavity Pumps
- Precision: Progressive cavity pumps provide accurate dosing, which is essential for processes requiring specific fluid quantities.
- Versatility: These pumps can handle a wide range of fluids, including those that are viscous, abrasive, or contain solids, making them suitable for various applications.
- Gentle Handling: The design of progressive cavity pumps minimizes shear, making them perfect for sensitive materials that could be damaged by high turbulence.
- Continuous Flow: The steady flow of these pumps ensures that the dosing process remains uninterrupted, enhancing overall efficiency.
- Self-Priming: Many progressive cavity pumps are self-priming, which simplifies the setup and operational processes.
Working Principles of Dosing with Progressive Cavity Pumps
The dosing process begins with the fluid entering the pump through the inlet. As the rotor turns, it creates a series of expanding cavities that move the fluid forward. The following steps outline how this process works:
- Fluid Intake: The pump draws in the fluid using the rotor’s movement.
- Cavity Formation: The helical design forms cavities that capture the fluid.
- Fluid Displacement: As the rotor continues to turn, these cavities move towards the outlet, displacing the fluid.
- Delivery: The fluid exits the pump at a controlled rate, allowing for precise dosing.
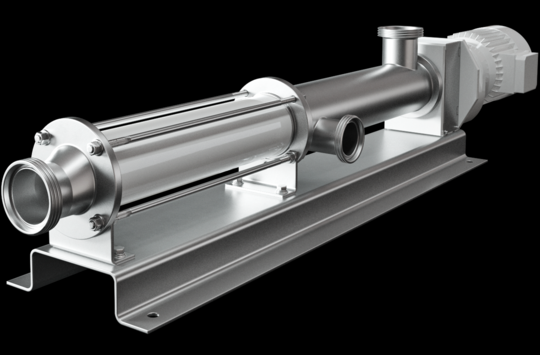
Considerations for Effective Dosing
To achieve optimal performance when using progressive cavity pumps for dosing, several factors should be considered:
- Viscosity of the Fluid: Ensure that the pump is suitable for the viscosity of the fluid being dosed.
- Calibration: Regular calibration is necessary to maintain accuracy in dosing.
- Maintenance: Routine maintenance helps prevent wear and tear, ensuring consistent performance.
- Compatibility: Verify that the materials of the pump are compatible with the fluid to avoid corrosion or degradation.
Conclusion
Dosing with progressive cavity pumps presents numerous advantages across various industries. Their ability to provide precise, continuous flow makes them an excellent choice for applications requiring accurate fluid delivery. By understanding their working principles and considering essential factors, users can maximize the efficiency and reliability of these pumps in their dosing processes.
People also ask
Send Your Enquiry :