Progressive cavity pumps are widely used fluid transfer devices in various industrial sectors, particularly in oil, chemical, and food industries. Their unique structure and operating principles meet the demands of transporting complex fluids. This article explores the API 676 standard for progressive cavity pumps, including their features, applications, advantages and disadvantages, as well as maintenance practices.
Features of Progressive Cavity Pumps
Progressive cavity pumps have several notable features:
- Continuous Flow: These pumps provide a consistent flow by gradually compressing the fluid, eliminating pulsation during operation.
- High Adaptability: They can handle a variety of viscous and non-Newtonian fluids, making them suitable for transporting fluids containing solid particles.
- Low Shear Force: The pumping process exerts minimal shear force on the fluid, making them ideal for shear-sensitive fluids such as emulsions and suspensions.
- High Efficiency: They maintain high efficiency over a wide flow range, helping to reduce energy consumption.
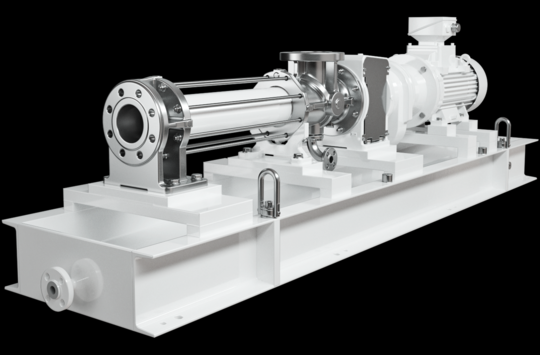
Applications
The applications of progressive cavity pumps are extensive and include the following areas:
- Oil and Gas: Used for pumping high-viscosity oil products and fluids containing gas in oil field extraction and gas transport.
- Chemical Industry: Suitable for transporting viscous liquids during chemical reactions, such as polymers, paints, and resins.
- Food and Beverage: Commonly used in food processing for transporting syrups, juices, and dairy products.
- Wastewater Treatment: Effective for conveying sewage and wastewater, handling fluids with high viscosity and solid particle content.
Advantages and Disadvantages
Advantages
- Simple Structure: Compared to other pump types, progressive cavity pumps have a simpler design, making maintenance easier.
- Strong Wear Resistance: With appropriate material selection for the pump body and rotor, these pumps exhibit good wear resistance and have a long service life.
- Adjustable Flow Rate: Flow rates can be flexibly controlled by adjusting the speed, accommodating varying operational requirements.
Disadvantages
- High Initial Cost: The initial investment for progressive cavity pumps is relatively high compared to other pump types.
- Temperature Sensitivity: Certain materials may deform at high temperatures, affecting pump performance.
- High Maintenance Requirements: While the structure is simple, the pump requires regular checks and maintenance for seals and lubrication.
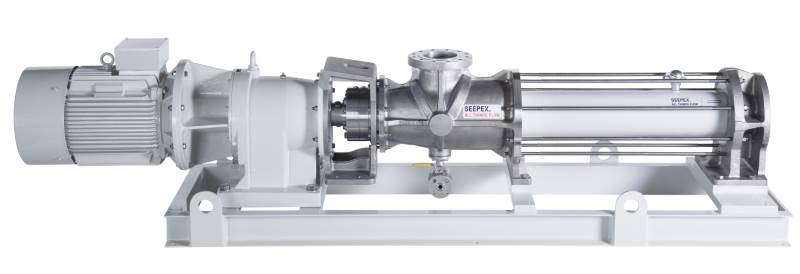
Maintenance and Care
Regular maintenance and care are essential to ensure the efficient operation of progressive cavity pumps. Here are some maintenance tips:
- Regularly Check Seals: Worn seals can lead to leaks, so regular inspection and replacement are necessary.
- Monitor Fluid Temperature and Viscosity: Regularly monitor the temperature and viscosity of the pumped fluid to ensure they are within acceptable ranges.
- Clean the Pump Body: Keep the pump body clean to prevent solid particle accumulation that could affect performance.
- Lubrication Maintenance: Regularly check the condition of lubricating oil to maintain good lubrication and prevent wear.
Conclusion
API 676 progressive cavity pumps play a crucial role in modern industry due to their unique operating principles and wide range of applications. Despite some drawbacks, their advantages make them an ideal solution for fluid transfer in specific environments. With proper maintenance and care, the lifespan of the pumps can be extended, ensuring efficient and stable operation.
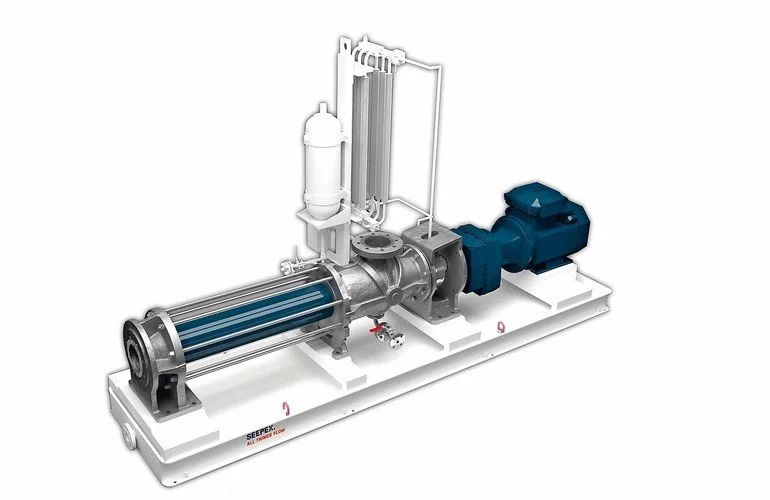
People also ask
Send Your Enquiry :