Progressive cavity pumps are widely used in the oil extraction industry due to their efficient liquid transfer capabilities. In oil well operations, controlling the pump’s back spin is crucial for ensuring proper fluid flow and enhancing extraction efficiency. This article explores the back spin control mechanisms in progressive cavity pumps and their applications in oil wells.
Working Principle of Progressive Cavity Pumps
Progressive cavity pumps consist of a rotor and a stator. As the rotor rotates inside the stator, it creates a continuous, progressively narrowing cavity. This design enables the pump to operate effectively with both low and high viscosity fluids. The efficiency of the pump is closely related to the rotor’s rotational speed, making proper back spin control essential.
Importance of Back Spin Control
In oil extraction, back spin control impacts several factors:
- Flow Stability: Adjusting the rotational speed allows for precise flow control, preventing equipment damage due to flow fluctuations.
- Energy Optimization: Proper rotational speed can reduce energy consumption, improve pump efficiency, and lower operational costs.
- Fluid Transfer Performance: Controlling the rotational speed helps enhance fluid transfer performance, minimizing bubble formation and increasing extraction efficiency.
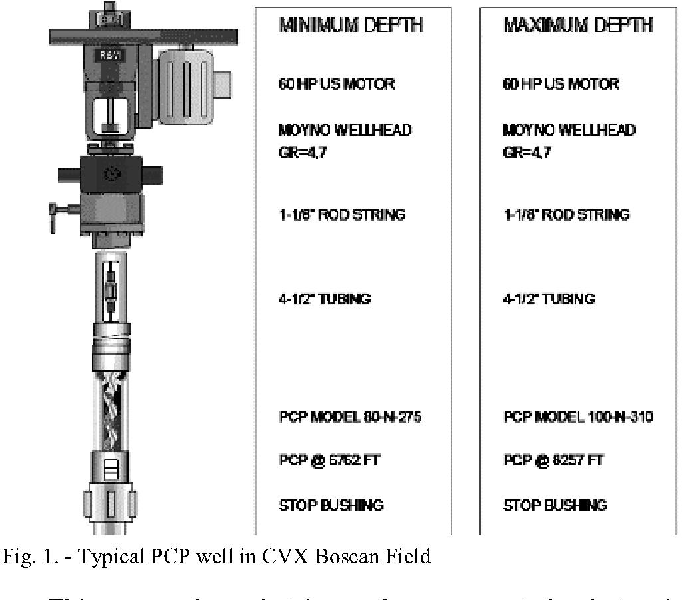
Methods of Implementing Back Spin Control
In progressive cavity pumps, several methods can be used to achieve back spin control:
1. Variable Frequency Drive
Variable frequency drive (VFD) technology adjusts the motor’s power supply frequency to achieve precise speed control. This method offers several advantages:
- High Flexibility: Speed can be adjusted as needed based on real-time requirements.
- Significant Energy Savings: Reduces unnecessary energy consumption, enhancing overall system efficiency.
2. Mechanical Adjustment
Mechanical adjustment involves changing the pump’s structural parameters to control the rotational speed. The pros and cons of this method include:
- Simplicity: Relatively easy to implement with low maintenance costs.
- Limited Adjustment Range: May not provide fine control, suitable for scenarios with lower flow requirements.
3. Automatic Feedback Control Systems
Using sensors to monitor the pump’s operating conditions in real time, combined with an automatic control system, allows for dynamic adjustments. This method has advantages such as:
- Real-Time Response: Quickly adapts to changes in fluid flow, maintaining stable flow rates.
- High Level of Intelligence: Can adapt to complex working environments, improving overall operational efficiency.
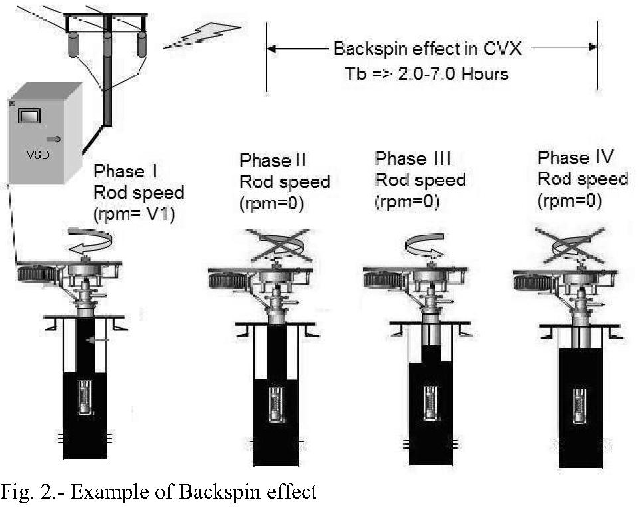
Challenges of Back Spin Control
Despite the importance of back spin control in progressive cavity pumps, several challenges arise in practical applications:
- System Complexity: Designing and maintaining automatic control systems require specialized knowledge, increasing operational costs.
- Environmental Adaptability: In extreme conditions, sensors and control systems may fail, disrupting normal pump operation.
- Variability of Fluid Properties: Differences in fluid characteristics across various oil wells may necessitate adjustments and optimization of control strategies.
Conclusion
Back spin control in progressive cavity pumps plays a vital role in enhancing extraction efficiency in oil wells while optimizing the entire operational process. By employing methods such as variable frequency drives, mechanical adjustments, and automatic feedback control systems, various challenges can be effectively addressed, ensuring high and stable pump performance. As technology continues to advance, back spin control is expected to become even more intelligent, further improving the efficiency and safety of oil extraction operations.
People also ask
Send Your Enquiry :