Pumps play a critical role in various industrial applications and everyday tasks, serving as essential devices for liquid transportation. However, one significant issue that can arise during pump operation is cavity formation, commonly known as cavitation. This phenomenon can severely affect pump performance and longevity. In this article, we will explore the causes, impacts, and preventive measures associated with cavity formation in pumps.
Understanding Cavitation
Cavitation occurs when vapor bubbles form in a liquid due to changes in pressure. These bubbles can appear in low-pressure zones within the pump or in the surrounding fluid. When the pressure in these areas drops below the vapor pressure of the liquid, vaporization occurs, leading to bubble formation. As the liquid flows into regions of higher pressure, these bubbles collapse violently, creating shock waves that can damage pump components.
Causes of Cavitation
- Fluid Dynamics
- High Flow Rates: Increased flow velocity can cause localized pressure drops, leading to cavitation.
- Viscosity: The viscosity of the liquid can influence flow resistance, potentially contributing to pressure variations.
- Design Flaws
- Pump Configuration: Inadequate design, such as mismatched inlet and outlet diameters, can result in uneven fluid flow.
- Impeller Design: An improperly designed impeller may not generate sufficient suction, increasing the likelihood of cavitation.
- Operational Conditions
- Low Liquid Levels: Insufficient liquid levels in the supply tank can prevent smooth liquid entry into the pump.
- High Ambient Temperature: Elevated temperatures can raise the vapor pressure of the liquid, making cavitation more likely.
- Liquid Characteristics
- Temperature and Composition: The physical properties of the liquid, particularly temperature, directly impact its vapor pressure, influencing cavitation potential.
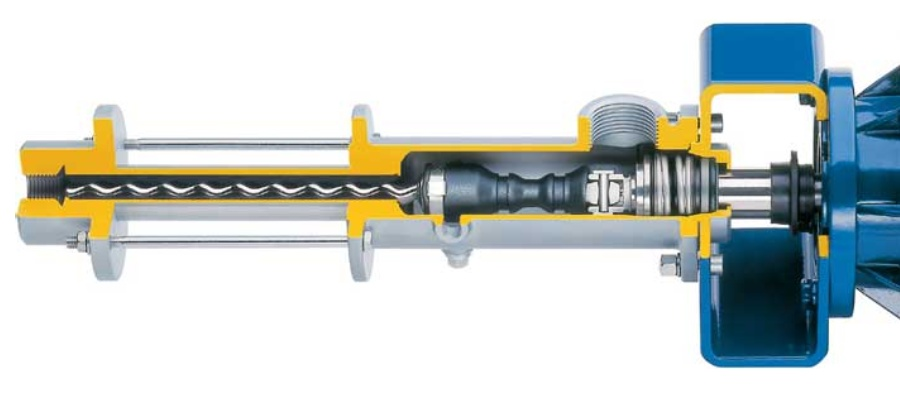
Impacts of Cavitation
- Decreased Performance
- Cavitation can lead to reduced flow rates and head, negatively affecting pump efficiency and output.
- Increased Wear and Tear
- The shock waves generated by collapsing bubbles can cause significant wear on impellers, casings, and other pump components, reducing their lifespan.
- Vibration and Noise
- Cavitation often results in abnormal vibrations and noise during pump operation, which can disrupt the working environment and indicate potential issues.
- Higher Maintenance Costs
- Frequent repairs or component replacements due to cavitation damage can lead to increased operational and maintenance costs.
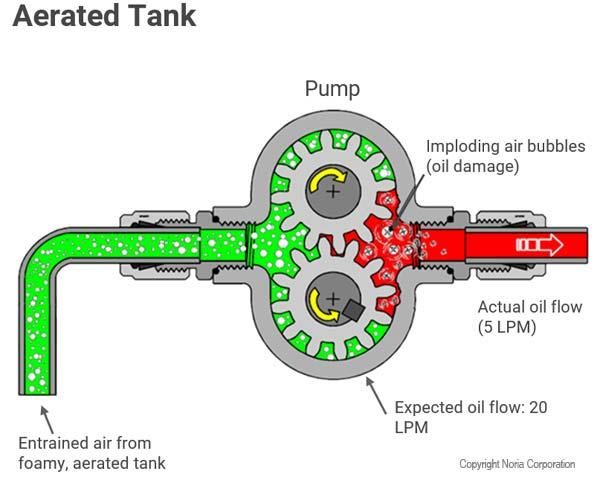
Preventive Measures
- Selecting the Right Pump Type
- Choosing a pump that suits the specific application and operating conditions helps ensure optimal performance and minimizes the risk of cavitation.
- Design Optimization
- During the design phase, incorporating fluid dynamics principles can lead to smoother flow paths and reduced resistance within the pump.
- Monitoring Operating Conditions
- Keeping an eye on the pump’s operational status, including fluid levels and inlet pressure, can help prevent conditions that lead to cavitation.
- Controlling Liquid Temperature
- Regulating the temperature of the liquid being pumped can lower vapor pressure, thereby reducing the likelihood of cavitation.
- Regular Maintenance
- Conducting routine checks and maintenance can catch potential issues early, ensuring that the pump runs efficiently and reducing the risk of cavitation-related damage.
Conclusion
Cavity formation, or cavitation, is a prevalent issue in pump operation that can significantly impact performance and lifespan. By understanding the causes and effects of cavitation, operators can implement effective preventive measures. Selecting the appropriate pump type, optimizing designs, monitoring operating conditions, controlling liquid temperatures, and conducting regular maintenance are all critical steps in mitigating the risks associated with cavitation. Through comprehensive management and care, the longevity and efficiency of pumps can be enhanced, ultimately leading to smoother operations and reduced costs.
People also ask
Send Your Enquiry :