Cavity pumps are essential in various industries for fluid handling. Understanding their specifications is crucial for selecting the right pump for specific applications. This article delves into the key specifications of cavity pumps, their components, and considerations for effective operation.
What is a Cavity Pump?
Cavity pumps, also known as progressive cavity pumps, utilize a helical rotor within a stator to move fluids. This design allows for a smooth, continuous flow, making them ideal for handling viscous and non-viscous liquids alike.
Key Specifications of Cavity Pumps
When selecting a cavity pump, several specifications must be considered to ensure optimal performance. Below are the primary specifications to evaluate:
1. Flow Rate
- Definition: The volume of fluid that can be moved by the pump in a specific time frame.
- Importance: Knowing the required flow rate is essential for selecting a pump that meets operational demands.
2. Pressure Rating
- Definition: The maximum pressure the pump can handle safely.
- Importance: The pressure rating determines the pump’s suitability for different applications, especially in high-pressure environments.
3. Viscosity Range
- Definition: The range of fluid thickness that the pump can efficiently handle.
- Importance: Cavity pumps excel in moving viscous fluids, but understanding the viscosity range helps in choosing the right model for specific fluids.

4. Temperature Tolerance
- Definition: The range of temperatures within which the pump can operate effectively.
- Importance: Different applications may involve extreme temperatures, making it critical to ensure the pump’s materials can withstand such conditions.
5. Material Construction
- Definition: The composition of the pump’s components, including the rotor and stator.
- Importance: The right materials are essential for durability and compatibility with the fluids being pumped, especially in corrosive environments.
6. Self-Priming Capability
- Definition: The pump’s ability to create suction and draw fluid without the need for external assistance.
- Importance: Self-priming pumps are beneficial in applications where fluid levels may fluctuate.
7. Efficiency
- Definition: The effectiveness of the pump in converting input energy into fluid movement.
- Importance: Higher efficiency translates to lower operational costs and reduced wear on pump components.
8. Noise Levels
- Definition: The amount of sound produced during operation.
- Importance: In environments where noise pollution is a concern, selecting a quieter pump can enhance working conditions.
Components of a Cavity Pump
Understanding the components of a cavity pump can provide insight into its operation and maintenance. Key components include:
- Rotor: The helical shape allows for fluid movement as it rotates within the stator.
- Stator: The stationary part that houses the rotor and creates a cavity for fluid transport.
- Drive Shaft: Connects the motor to the rotor, enabling rotation.
- Seals: Prevent leakage and protect the internal components from external contaminants.
- Bearing: Supports the rotor and ensures smooth operation.
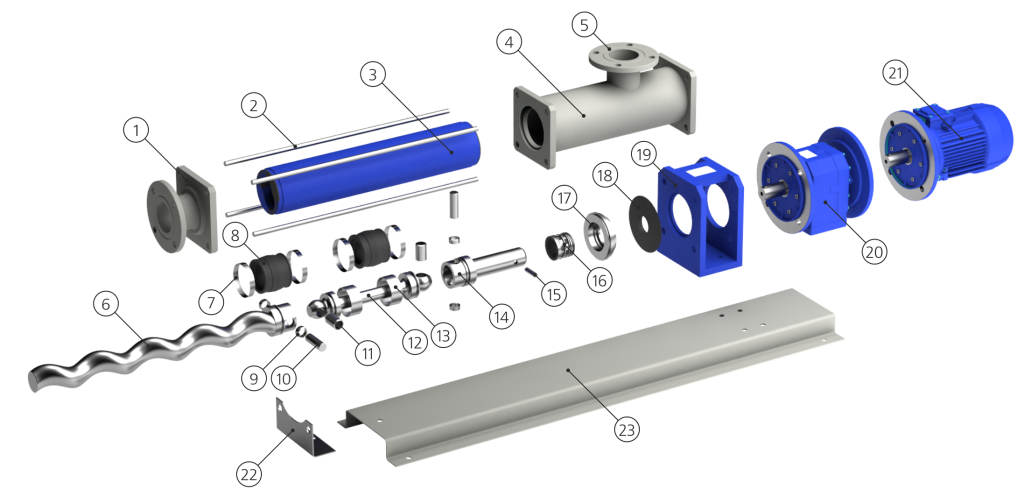
Considerations for Effective Operation
To ensure that a cavity pump performs optimally, consider the following factors:
- Proper Sizing: Ensure that the pump is appropriately sized for the intended application to avoid inefficiencies.
- Regular Maintenance: Schedule routine inspections and maintenance to extend the pump’s lifespan and maintain performance.
- Monitoring Conditions: Keep an eye on operating conditions such as pressure, temperature, and viscosity to detect potential issues early.
- Fluid Compatibility: Always verify that the pump materials are compatible with the fluids being handled to prevent corrosion or degradation.
Conclusion
Cavity pumps play a vital role in fluid handling across various industries. By understanding their specifications, components, and operational considerations, users can make informed decisions when selecting a cavity pump for their specific needs. Proper attention to these details will ensure reliable performance and longevity, ultimately contributing to the efficiency of industrial processes.
People also ask
Send Your Enquiry :