Crude oil transfer is a critical process in the oil and gas industry, involving the movement of crude oil from one location to another. This process is vital for refining, transportation, and storage. One of the key technologies employed in this operation is the sludge progressive cavity pump. This article explores the significance of crude oil transfer and the advantages of using progressive cavity pumps in handling sludge.
Importance of Crude Oil Transfer
Crude oil is a primary energy source worldwide, and its efficient transfer is essential for several reasons:
- Supply Chain Efficiency: Smooth transfer operations are crucial for maintaining an uninterrupted supply chain within the oil and gas sector.
- Cost Management: Efficient transfer processes can significantly reduce operational costs by minimizing losses and downtime.
- Safety and Environmental Protection: Proper handling of crude oil minimizes the risk of spills and environmental hazards, ensuring safer operations.
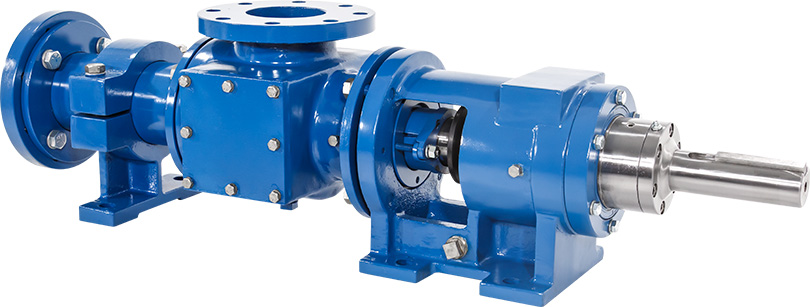
Understanding Sludge Progressive Cavity Pumps
Progressive cavity pumps are positive displacement pumps that are particularly well-suited for transferring viscous fluids, including sludge. They consist of a helical rotor and stator, which create cavities that progressively move the fluid through the pump. This design offers several advantages for crude oil transfer:
Advantages of Progressive Cavity Pumps
- High Efficiency: These pumps maintain a consistent flow rate, ensuring that crude oil and sludge are transferred efficiently, even under varying viscosity conditions.
- Versatility: Progressive cavity pumps can handle a wide range of fluids, making them suitable for transferring crude oil mixed with sludge or other contaminants.
- Low Shear Rate: The gentle pumping action reduces the risk of damaging sensitive components within the fluid, preserving the quality of the crude oil.
- Self-Priming Capability: These pumps can effectively manage air and gas pockets, making them ideal for challenging transfer scenarios.
- Durability: Constructed from robust materials, progressive cavity pumps can withstand the corrosive nature of crude oil and sludge, ensuring a long operational life.
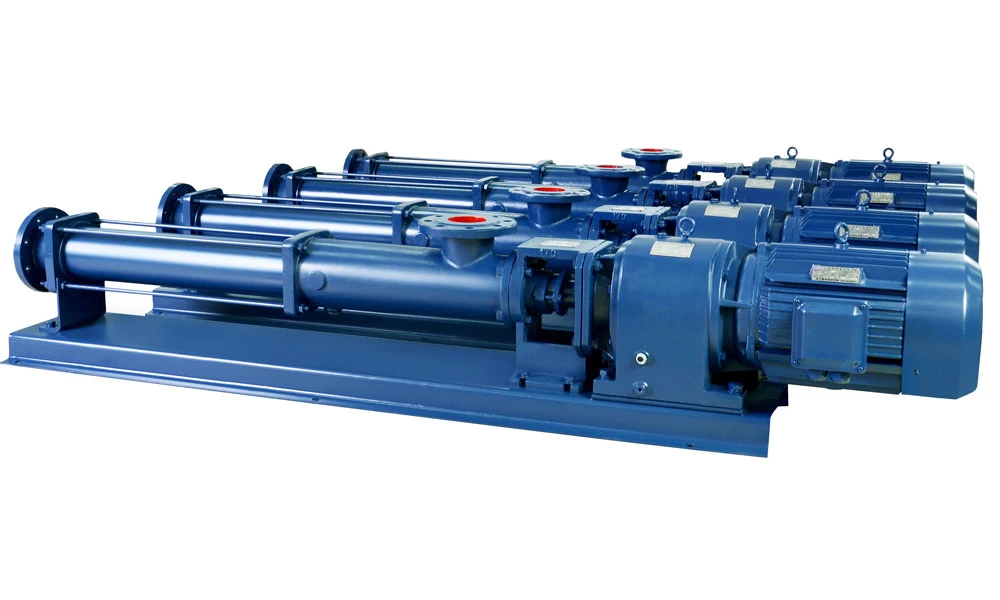
Applications in Crude Oil Transfer
Progressive cavity pumps are widely utilized in various stages of crude oil transfer, including:
- Production Facilities: Moving crude oil from extraction points to storage tanks.
- Refineries: Transferring crude oil to processing units while handling sludge generated during refining.
- Transportation: Loading and unloading crude oil from tankers and pipelines, often encountering mixed sludge.
Conclusion
In the realm of crude oil transfer, the importance of utilizing effective pumping solutions cannot be overstated. Sludge progressive cavity pumps offer a reliable, efficient, and versatile option for handling the complexities of crude oil and sludge transfer. Their unique design and operational capabilities make them an invaluable asset in ensuring the smooth operation of the oil and gas industry. As the demand for crude oil continues to grow, so does the need for advanced pumping technologies that can meet the challenges of this dynamic sector.
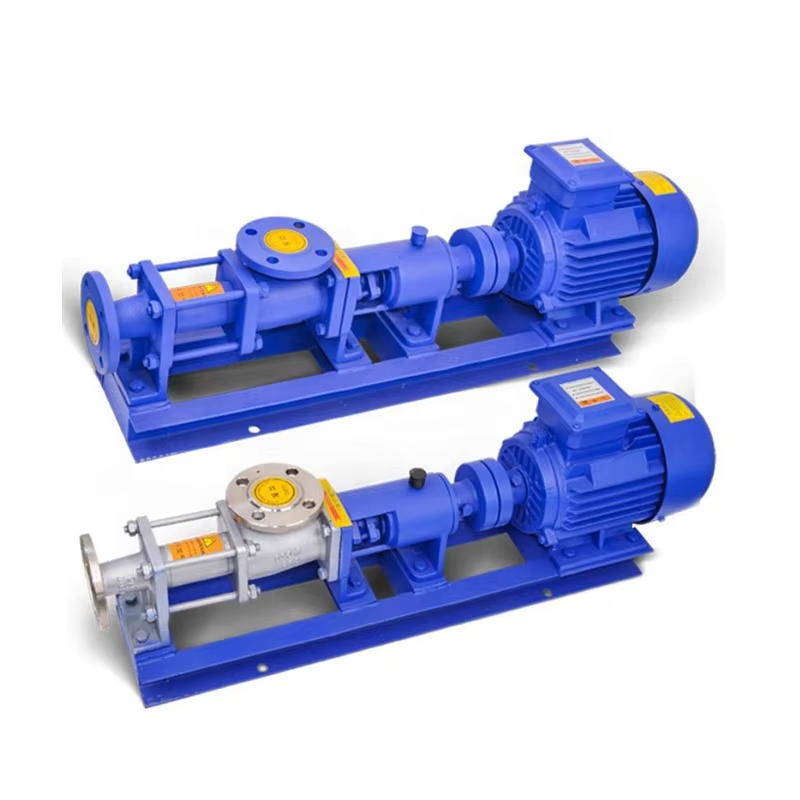
People also ask
Send Your Enquiry :