Progressive cavity pumps are widely used for transferring viscous fluids in various industries. Their unique design allows for efficient handling of challenging materials, making them a preferred choice in many applications. This article will explore the key aspects of designing progressive cavity pumps, including their components, working principle, advantages, and considerations in the design process.
Components of Progressive Cavity Pumps
The design of a progressive cavity pump consists of several critical components:
- Rotor: A helical screw that rotates within the stator, creating cavities that transport the fluid.
- Stator: A stationary component that surrounds the rotor, usually made of elastomeric material, providing a seal that helps maintain pressure.
- Drive Shaft: Connects the rotor to the motor, allowing for rotation.
- Bearings: Support the rotor and minimize friction during operation.
- Hopper: Often included for handling solids or slurries, ensuring smooth entry into the pump.
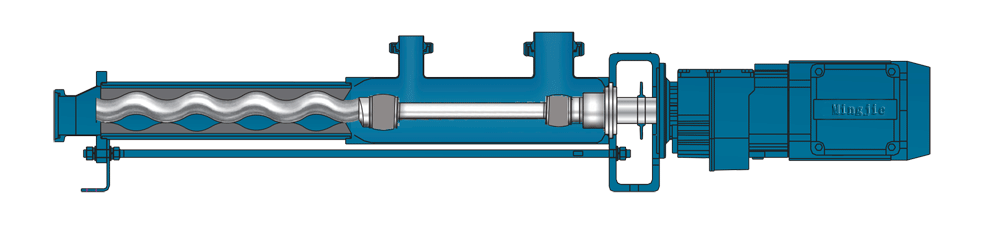
Working Principle
The fundamental working principle of progressive cavity pumps revolves around the movement of the rotor within the stator. As the rotor turns, it moves the fluid through a series of cavities formed between the rotor and stator. This continuous movement creates a consistent flow, making it suitable for transferring fluids with varying viscosities.
Key Features of Operation
- Non-Pulsating Flow: The design allows for a smooth and continuous flow, reducing wear on the pump and associated piping.
- Self-Priming Capability: The pump can draw fluid into the system without the need for external priming.
- Versatile Handling of Fluids: It can manage shear-sensitive, abrasive, or viscous fluids effectively.
Advantages of Progressive Cavity Pumps
The design of progressive cavity pumps offers several advantages that enhance their utility across different applications:
- Efficiency: High volumetric efficiency ensures minimal energy loss during operation.
- Durability: Robust construction and materials allow for long service life, even in harsh environments.
- Adaptability: Capable of handling a wide range of fluids, including those with solid content.
- Easy Maintenance: Simplified design allows for straightforward maintenance and repairs.
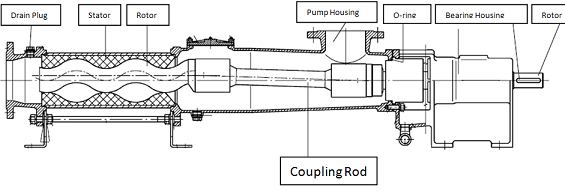
Design Considerations
When designing a progressive cavity pump, several factors must be taken into account to ensure optimal performance:
- Material Selection: Choosing appropriate materials for the rotor and stator is crucial for durability and compatibility with the fluid being pumped.
- Viscosity and Temperature: Understanding the properties of the fluid will help in selecting the right pump configuration and components.
- Pump Size and Capacity: The design should align with the specific flow requirements of the application, taking into consideration the space available for installation.
- Seal Integrity: Ensuring proper sealing is vital to prevent leaks and maintain efficiency.
Conclusion
The design of progressive cavity pumps is a complex yet rewarding process that requires careful consideration of various factors. By understanding the components, working principles, advantages, and design considerations, engineers can create efficient and reliable pumps suited for diverse applications. Whether in wastewater treatment, food processing, or chemical manufacturing, progressive cavity pumps play a vital role in ensuring smooth and effective fluid transfer.
People also ask
Send Your Enquiry :