Introduction
In the world of fluid transfer and pumping solutions, the high pressure progressive cavity pump stands out for its unique design and operational efficiency. This type of pump is widely used across various industries, including oil and gas, food processing, and wastewater treatment. Its ability to handle viscous fluids and maintain a consistent flow makes it an invaluable asset in many applications.
How It Works
The high pressure progressive cavity pump operates based on a helical rotor and stator mechanism. As the rotor turns within the stator, it creates a series of cavities that move fluid from the inlet to the outlet. This design allows for a smooth, continuous flow, minimizing pulsation and pressure fluctuations.
Key Components:
- Rotor: The rotating element that moves the fluid.
- Stator: The stationary part that surrounds the rotor, creating cavities.
- Drive Shaft: Connects the rotor to a motor, providing the necessary power for operation.
- Bearing Assembly: Supports the rotor and ensures smooth rotation.
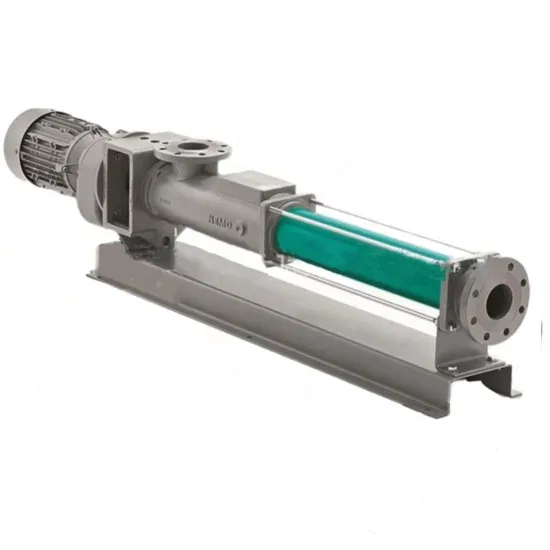
Advantages
The high pressure progressive cavity pump offers several advantages that make it a preferred choice for many applications:
- Versatility: Capable of handling a wide range of fluids, including viscous, shear-sensitive, and abrasive materials.
- Consistent Flow: Delivers a steady flow rate, making it ideal for applications requiring precise fluid transfer.
- Self-Priming: Can efficiently handle air and gas entrained fluids, reducing the need for additional equipment.
- Durability: Designed for long-term use under high pressure conditions, reducing maintenance requirements.
Applications
The versatility of high pressure progressive cavity pumps allows them to be used in various sectors:
- Oil and Gas: Ideal for transporting crude oil, sludge, and other viscous materials.
- Food Processing: Suitable for handling food products, such as sauces, pastes, and dairy products, without compromising quality.
- Wastewater Treatment: Efficiently moves sludge and other byproducts, ensuring effective waste management.
- Chemical Processing: Handles aggressive chemicals safely and reliably.
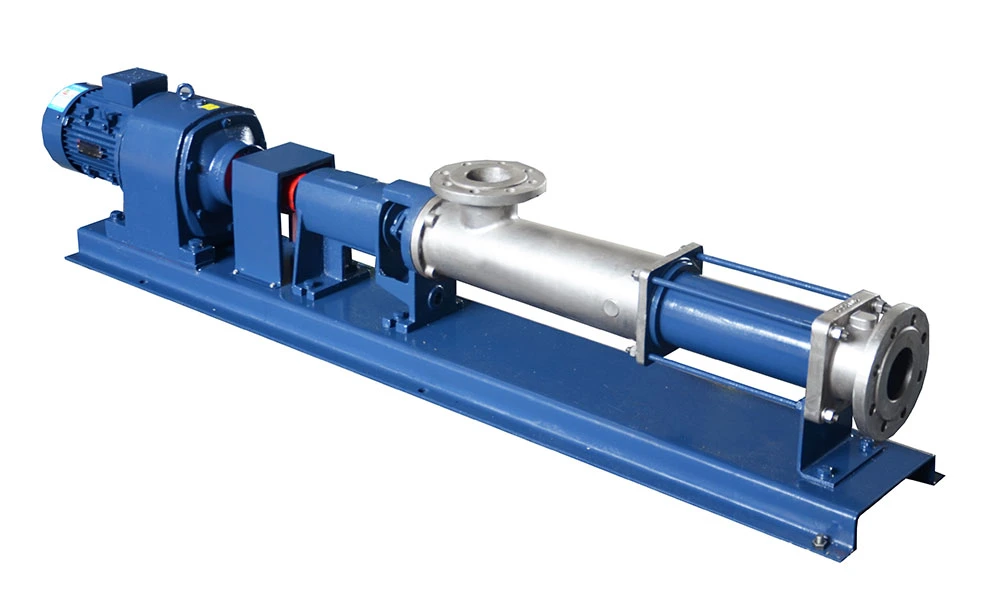
Maintenance Considerations
To ensure optimal performance and longevity, regular maintenance is essential. Here are some key maintenance tips:
- Routine Inspections: Regularly check for wear and tear on components, especially the rotor and stator.
- Lubrication: Ensure proper lubrication of bearings and moving parts to minimize friction and wear.
- Monitor Performance: Keep an eye on flow rates and pressure levels to detect any abnormalities early.
- Cleaning: Periodically clean the pump to prevent buildup of materials that could affect performance.
Conclusion
The high pressure progressive cavity pump is a robust and reliable solution for various fluid transfer needs. Its unique design, coupled with numerous advantages, makes it an essential tool in many industries. By understanding its operation, applications, and maintenance requirements, users can maximize the efficiency and lifespan of this invaluable equipment.
People also ask
Send Your Enquiry :