Progressive cavity pumps are a vital component in many industrial applications, particularly when it comes to handling viscous fluids and slurries. These pumps are designed to operate efficiently under high pressure, making them ideal for a variety of demanding environments. In this article, we will explore the key features, advantages, and applications of high pressure progressive cavity pumps.
What are Progressive Cavity Pumps?
Progressive cavity pumps consist of a helical rotor that rotates within a stator. The unique design allows for a continuous and smooth flow of fluid, which is particularly beneficial when dealing with materials that are thick or contain solids. The rotor and stator work together to create cavities that transport the fluid from the inlet to the outlet.
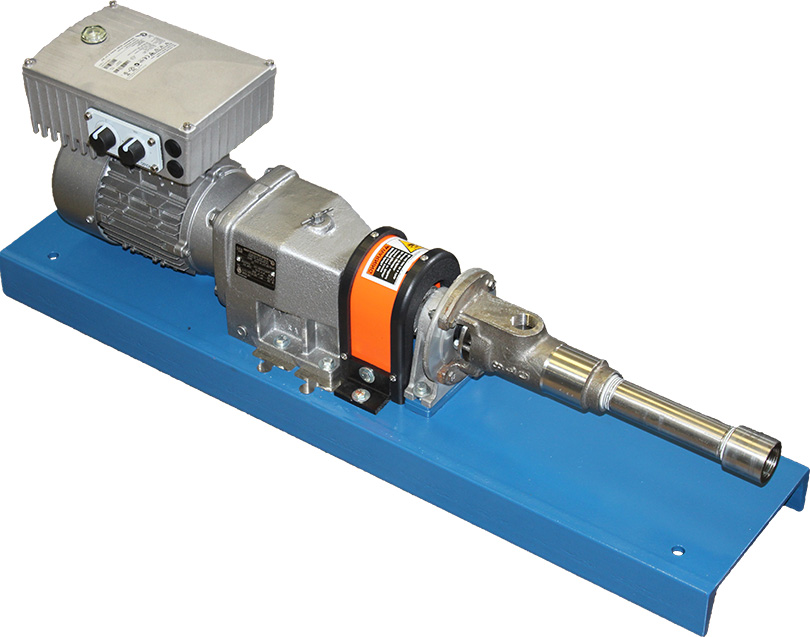
Key Features
- High Pressure Capability: These pumps are engineered to handle high pressure, making them suitable for applications that require robust performance.
- Versatility: Progressive cavity pumps can handle a wide range of fluids, including those that are abrasive, viscous, or contain solids.
- Continuous Flow: The design allows for a smooth and continuous flow, reducing pulsations and ensuring consistent delivery of the fluid.
- Self-Priming: Many models are self-priming, which simplifies the installation process and enhances operational efficiency.
Advantages of High Pressure Progressive Cavity Pumps
- Efficiency: These pumps are highly efficient and can maintain performance over long periods, reducing the need for frequent maintenance.
- Durability: Constructed with robust materials, they are designed to withstand harsh conditions and prolong service life.
- Low Shear: The gentle pumping action minimizes shear stress on the fluid, making it ideal for sensitive materials that could be damaged by other types of pumps.
- Easy Maintenance: With fewer moving parts, maintenance is straightforward, allowing for quick repairs and reduced downtime.
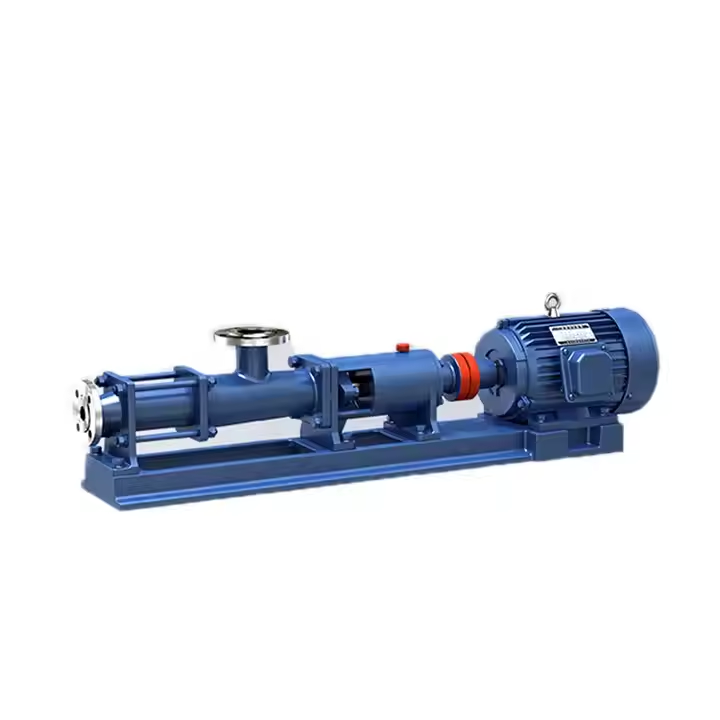
Applications
High pressure progressive cavity pumps are used in a variety of sectors, including:
- Oil and Gas: For transporting crude oil, emulsions, and chemicals.
- Food and Beverage: Handling viscous products like sauces, creams, and dough.
- Wastewater Treatment: For pumping sludge and other thick materials.
- Chemical Processing: Involved in the transfer of corrosive and viscous chemicals.
Conclusion
High pressure progressive cavity pumps offer a reliable solution for handling challenging fluids in various industries. Their unique design and operational capabilities make them an essential tool for ensuring efficiency and consistency in fluid transfer applications. As industries continue to innovate and demand more from their pumping systems, progressive cavity pumps will play a crucial role in meeting these needs.
People also ask
Send Your Enquiry :