Progressive cavity pumps are becoming increasingly popular in various industries due to their unique design and efficient performance. One of the leading brands in this field is Knoll, known for its innovative solutions and reliable products. This article will explore the features, benefits, and applications of Knoll progressive cavity pumps.
What Are Progressive Cavity Pumps?
Progressive cavity pumps are positive displacement pumps that utilize a helical rotor and a stator to move fluids. The rotor turns within the stator, creating cavities that progressively transport the fluid from the inlet to the outlet. This design allows for a smooth and continuous flow, making them ideal for handling viscous and shear-sensitive substances.

Key Features of Knoll Progressive Cavity Pumps
- Robust Construction
Knoll pumps are engineered with durable materials that withstand harsh operating conditions. This ensures long-lasting performance and reduces maintenance needs. - Versatile Applications
These pumps are suitable for a wide range of fluids, including slurries, chemicals, and food products. Their adaptability makes them valuable in various sectors. - Low Shear Handling
The gentle pumping action minimizes shear stress on the fluid, which is particularly important for sensitive materials like polymers and food products. - Variable Flow Rates
Knoll pumps can be easily adjusted to accommodate different flow requirements, providing flexibility in operations. - Self-Priming Capability
Many models feature self-priming capabilities, allowing for easy installation and operation without the need for additional equipment.
Benefits of Using Knoll Progressive Cavity Pumps
- Efficiency
The design of Knoll pumps ensures a consistent flow rate, reducing energy consumption and operational costs. - Reduced Maintenance
The simplicity of the rotor and stator design leads to fewer moving parts, which translates to lower maintenance requirements and downtime. - Improved Reliability
Knoll’s commitment to quality results in highly reliable pumps that can operate continuously in demanding environments. - Enhanced Performance
With the ability to handle a variety of fluids, these pumps deliver superior performance in diverse applications.
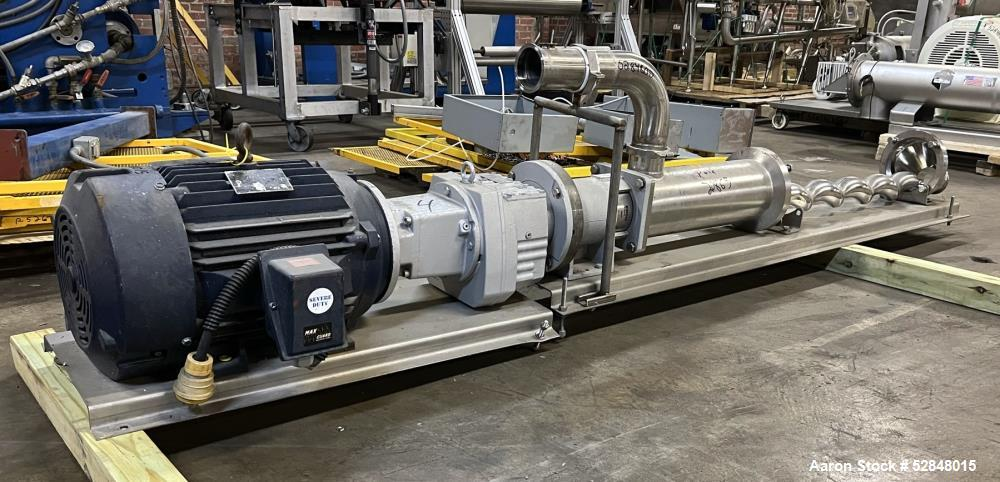
Common Applications
Knoll progressive cavity pumps are used in numerous industries, including:
- Food and Beverage
Ideal for transferring viscous products like sauces, creams, and pastes without altering their quality. - Chemical Processing
Efficiently handles corrosive and abrasive materials, ensuring safety and reliability in chemical applications. - Wastewater Treatment
Effective for pumping sludge and other viscous waste, contributing to efficient treatment processes. - Pharmaceuticals
Ensures precise dosing and transfer of sensitive substances, maintaining product integrity.
Conclusion
Knoll progressive cavity pumps stand out for their robust design, versatility, and efficiency. As industries continue to evolve, these pumps remain a reliable choice for managing various fluids. Their ability to operate in challenging environments while minimizing maintenance makes them an essential tool for many applications. Embracing Knoll’s innovative pumping solutions can lead to improved performance and reduced operational costs in any industrial setting.
People also ask
Send Your Enquiry :