Introduction
Low-shear progressive cavity pumps are essential devices in various industries, known for their unique design and functional capabilities. These pumps are widely used for handling viscous fluids, providing a gentle pumping action that minimizes shear stress on the material being transferred. This article explores the working principle, advantages, applications, and maintenance considerations of low-shear progressive cavity pumps.
Working Principle
The low-shear progressive cavity pump operates using a helical screw mechanism. It consists of two main components: a rotor and a stator. The rotor, which is typically made of metal, rotates within the stator, which is lined with an elastomeric material. As the rotor turns, it creates cavities that progressively move the fluid from the inlet to the outlet.
Key Features
- Gentle Pumping Action: The design minimizes turbulence, making it ideal for shear-sensitive materials.
- Self-Priming Capability: These pumps can handle fluids with varying viscosities and are capable of self-priming.
- Variable Flow Rates: The speed of the rotor can be adjusted to achieve different flow rates, providing flexibility in operation.
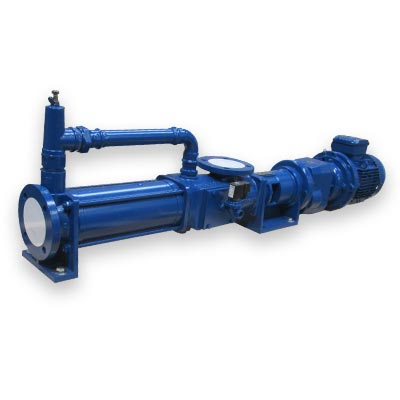
Advantages
Low-shear progressive cavity pumps offer several benefits that make them a preferred choice for many applications:
- Versatility: Suitable for a wide range of fluids, including slurries, emulsions, and solids-laden liquids.
- Consistency: Provides a steady flow rate, ensuring reliable performance in various processes.
- Durability: Constructed with robust materials, these pumps can withstand harsh operating conditions.
- Low Maintenance: With fewer moving parts compared to other pump types, maintenance requirements are significantly reduced.
Applications
These pumps find applications across various sectors, including:
- Food and Beverage Industry: Ideal for transferring sensitive products like creams, sauces, and juices without compromising quality.
- Chemical Processing: Used for handling aggressive chemicals and viscous materials in a controlled manner.
- Wastewater Management: Effective for pumping sludge and other thick mixtures in treatment facilities.
- Pharmaceuticals: Ensures gentle handling of sensitive formulations, maintaining product integrity.
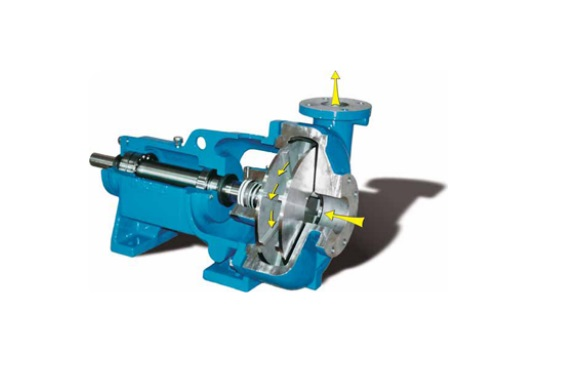
Maintenance Considerations
To ensure optimal performance and longevity of low-shear progressive cavity pumps, regular maintenance is crucial. Here are some key maintenance tips:
- Routine Inspections: Regularly check for wear and tear on the rotor and stator.
- Seal Checks: Inspect seals to prevent leaks and maintain efficiency.
- Lubrication: Ensure proper lubrication of moving parts to reduce friction and wear.
- Cleaning: Periodically clean the pump to prevent buildup of materials that could affect performance.
Conclusion
Low-shear progressive cavity pumps are invaluable in various industries due to their gentle pumping action and versatility. By understanding their working principles, advantages, applications, and maintenance needs, operators can maximize their efficiency and ensure smooth operations. These pumps play a critical role in maintaining the quality and integrity of sensitive fluids, making them a reliable choice for many applications.
People also ask
Send Your Enquiry :