vertical pump screw vs progressive cavity
When comparing vertical screw pumps and progressive cavity pumps, it’s important to understand their design, operation, and typical applications. Here’s a breakdown of the two types:
Vertical Screw Pumps
Design and Operation:
-
- Mechanism: Vertical screw pumps use a helical screw mechanism to move fluids. The screw rotates within a casing, creating a suction effect that draws fluid in and pushes it upward.
-
- Configuration: Typically installed vertically, these pumps are often used for handling large volumes of fluids.
Applications:
-
- Common Uses: Often found in water and wastewater treatment, agricultural irrigation, and industrial processes for transferring viscous fluids.
-
- Advantages: Good for lifting fluids from deep sources and handling solids or slurries without clogging.
Disadvantages:
-
- Efficiency: May not be as efficient for low-viscosity fluids compared to other types.
-
- Maintenance: Can require more maintenance due to wear on the screw and casing.
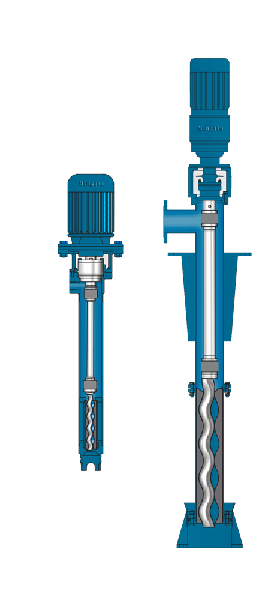
Progressive Cavity Pumps
Design and Operation:
-
- Mechanism: Progressive cavity pumps feature a helical rotor that rotates within a stator. This design creates multiple sealed cavities that transport fluid as the rotor turns.
-
- Configuration: Can be installed horizontally or vertically, making them versatile in various setups.
Applications:
-
- Common Uses: Widely used in industries such as oil and gas, food processing, and chemical manufacturing for handling thick and viscous materials.
-
- Advantages: Excellent for precise flow control and can handle a wide range of viscosities and solids without damage.
Disadvantages:
-
- Wear: The rotor and stator can wear over time, especially with abrasive fluids.
-
- Cost: Typically more expensive than some other pump types.
Summary
-
- Vertical Screw Pumps are ideal for lifting and transferring large volumes of fluids, especially in wastewater and agricultural applications.
-
- Progressive Cavity Pumps excel in moving viscous fluids with precise control and are versatile in various industrial applications.
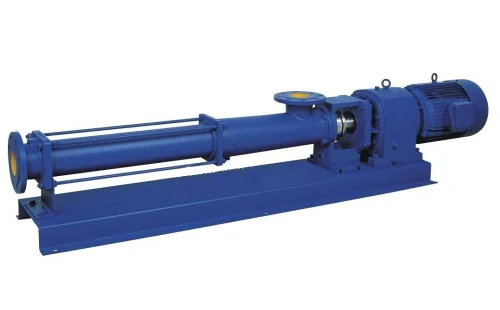
Choosing between the two depends on the specific requirements of your application, such as fluid type, viscosity, and flow rate needs.