In the industrial and engineering sectors, progressive cavity pumps (PCPs) are gaining significant attention due to their unique design and superior performance. The working principle and wide application range of these pumps make them essential equipment in many industries. This article explores the basic concepts, working principles, main features, and common applications of progressive cavity pumps.
What is a Progressive Cavity Pump?
A progressive cavity pump is a type of positive displacement pump primarily composed of a rotor and a stator. The rotor is a helical component, while the stator is a rubber tube with a similarly shaped internal wall. As the rotor rotates within the stator, liquid is gradually pushed toward the pump’s outlet. Due to its special structure, the progressive cavity pump can effectively handle various viscous liquids and solid particles.
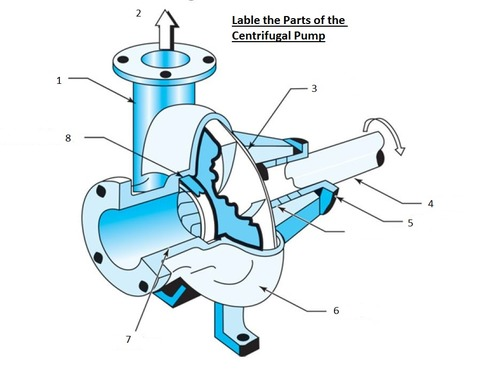
Working Principle
The working principle of a progressive cavity pump is relatively straightforward and can be broken down into several steps:
- Suction Phase: As the rotor rotates, liquid is drawn into the pump through the inlet. During this phase, the space between the rotor and stator gradually increases, creating negative pressure that allows the liquid to flow in.
- Transport Phase: With continuous rotation of the rotor, the liquid is progressively pushed through the helical cavity of the stator. The rotation of the rotor moves the liquid toward the pump outlet.
- Discharge Phase: Finally, the liquid is expelled through the pump’s outlet, completing the entire cycle.
This design allows progressive cavity pumps to deliver a stable flow rate, minimally affected by viscosity and pressure.
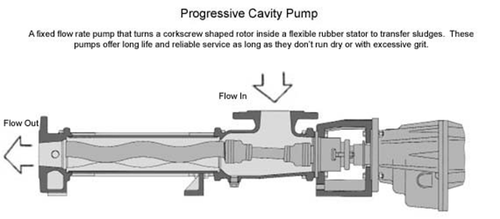
Main Features
Progressive cavity pumps have several notable features that enable them to perform excellently across various applications:
- Efficiency: These pumps can operate at low speeds, reducing energy consumption and enhancing efficiency.
- Handling Viscous Liquids: They are especially suitable for transporting high-viscosity and non-Newtonian fluids, such as oils and slurries.
- Reduced Pulsation: Due to their continuous flow characteristics, progressive cavity pumps effectively minimize pulsation in fluid transport, providing a smoother flow.
- Strong Adaptability: They can be customized with different materials and designs to meet diverse application requirements, adapting to various working conditions.
- Easy Maintenance: With a simple structure, progressive cavity pumps are relatively easy to maintain and replace parts, helping reduce downtime.
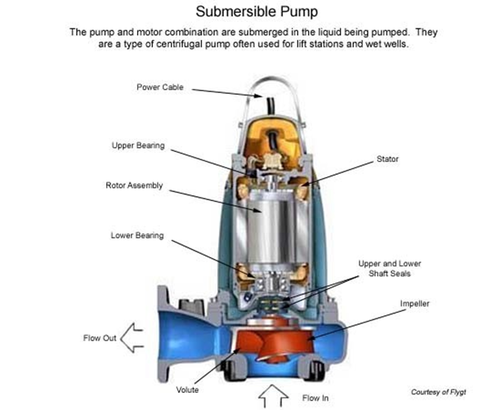
Application Areas
The application areas for progressive cavity pumps are vast, spanning multiple industries. Here are some common fields of application:
- Oil and Gas: Used for extracting and transporting crude oil and natural gas in oil fields.
- Chemical Industry: Employed for pumping various chemicals, including acids, bases, and solvents.
- Food and Beverage: Used in food processing to transport viscous liquids such as syrups and oils.
- Wastewater Treatment: Effective in handling wastewater and sewage, especially when dealing with liquids containing solid particles.
- Pharmaceutical Industry: Utilized in pharmaceutical processes to transfer various drugs and raw materials.
Conclusion
Progressive cavity pumps, with their unique design and efficient performance, have become indispensable equipment in many industries. Whether in oil, chemicals, food, or pharmaceuticals, these pumps demonstrate their exceptional transport capabilities and adaptability. As technology continues to advance, the application prospects for progressive cavity pumps are likely to expand even further, providing robust support for the development of various sectors.
people also ask
Send Your Enquiry :