Working Principle
The core working principle of the screw pump is to use the rotational motion of the screw to transport fluid. Its structure usually consists of one or more screws and a fixed pump housing. As the screw rotates, the fluid is gradually pushed between the screw and the pump housing, thereby achieving continuous fluid transportation.
Main Components
Screw: responsible for pushing the fluid, usually made of wear-resistant materials to extend service life.
Pump housing: provides a channel for fluid flow, usually made of high-strength materials.
Drive: provides power for the screw, common ones are electric motors and diesel engines.
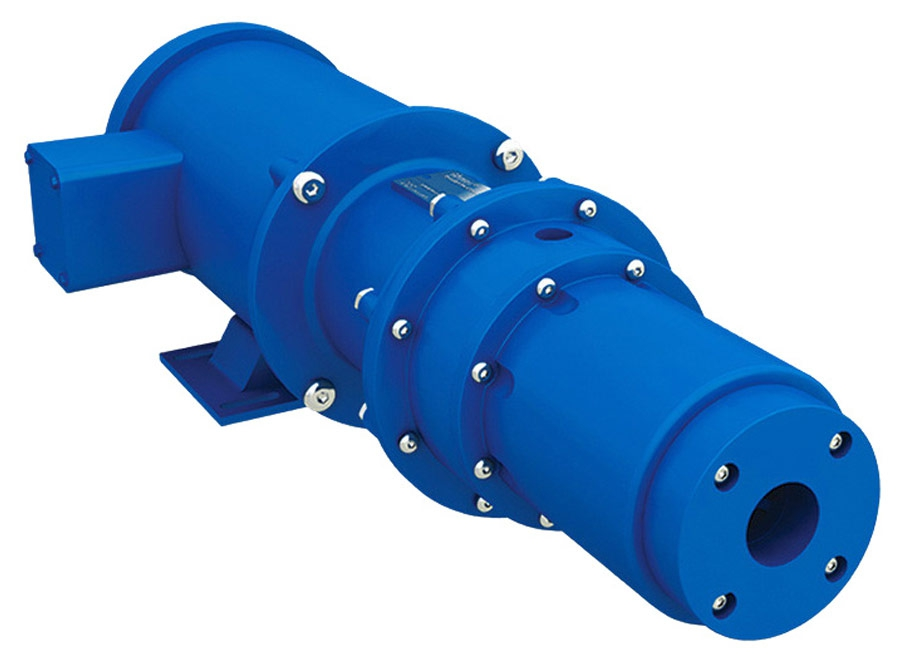
Application Areas
100 GPM screw pumps are widely used in the following fields due to their efficient fluid transportation capabilities:
Oil and Gas
Used for pressurized transmission of viscous oil and natural gas.
Chemical Industry
Suitable for the transportation of various chemical substances, especially viscous liquids and slurries.
Water Treatment
Commonly used for fluid transportation in sewage treatment and water resource recovery.
Food and Beverage
In food processing, it is responsible for the transportation of various liquids and slurries to ensure food safety.
Agricultural irrigation
Used to transport fertilizer liquid and pesticides to improve irrigation efficiency.
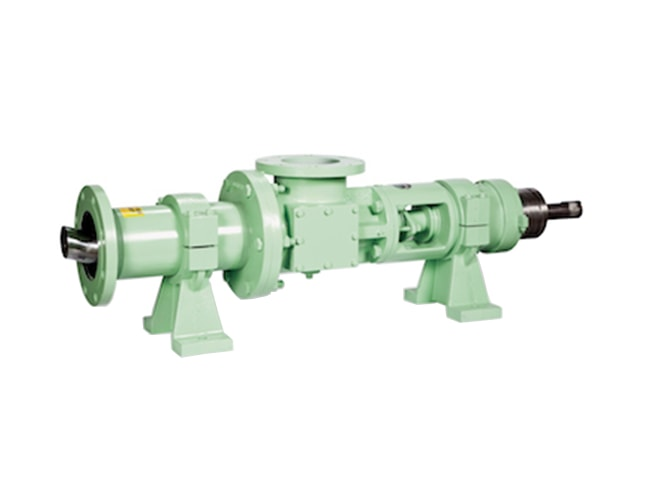
Advantages of progressive cavity pumps
Using progressive cavity pumps has many advantages:
Efficient delivery: It can transport various fluids, especially high-viscosity fluids, at a stable flow rate.
Good self-priming ability: It can achieve self-priming under certain conditions, reducing the need for other auxiliary equipment.
Strong adaptability: It does not require high properties of the fluid and can handle complex fluids containing particles, bubbles, etc.
Simple maintenance: The pump has a simple structure, and maintenance and maintenance are relatively easy, reducing operating costs.
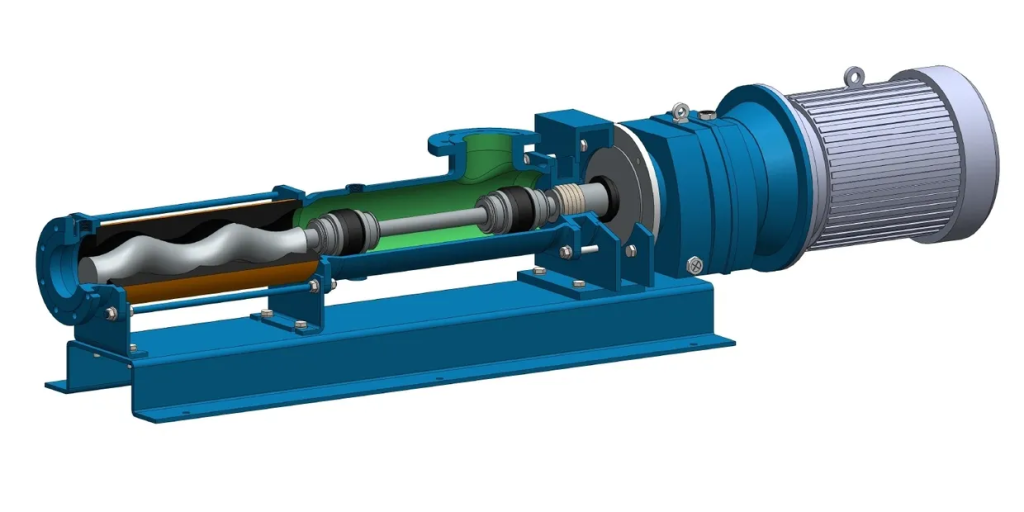
Precautions for selecting progressive cavity pumps
When selecting a progressive cavity pump, the following factors need to be considered:
Fluid properties: Understand the viscosity, temperature and particle content of the fluid being transported to select a suitable pump type.
Working conditions: Consider the installation environment of the pump, including temperature, pressure and space restrictions.
Material selection: According to the corrosiveness and temperature requirements of the fluid, select suitable materials to extend the service life of the pump.
Service support: Choose a supplier with good after-sales service and technical support to ensure the normal operation of the pump.
people also ask
Send Your Enquiry :