screw pump
A screw pump, also known as a progressive cavity pump, is a type of positive displacement pump that uses a rotating helical screw to move fluid through the pump. The key components of a screw pump include:
-
- Rotor: A single-threaded helical rotor that rotates inside the pump.
-
- Stator: A double-threaded helical casing that surrounds the rotor.
-
- Sealing Elements: These help maintain the seal between the rotor and stator, preventing leakage.
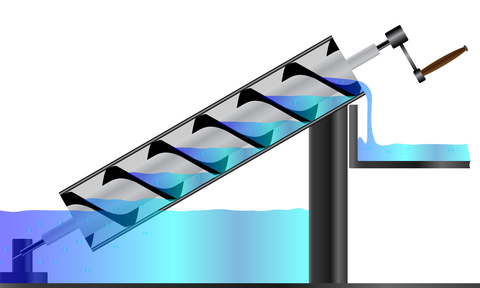
The operation of a screw pump can be summarized as follows:
-
- As the rotor rotates, it creates a series of sealed cavities between the rotor and the stator.
-
- These cavities move along the length of the pump, from the inlet to the outlet, carrying the fluid with them.
-
- The helical shape of the rotor and stator helps to create a smooth, continuous flow of the fluid.
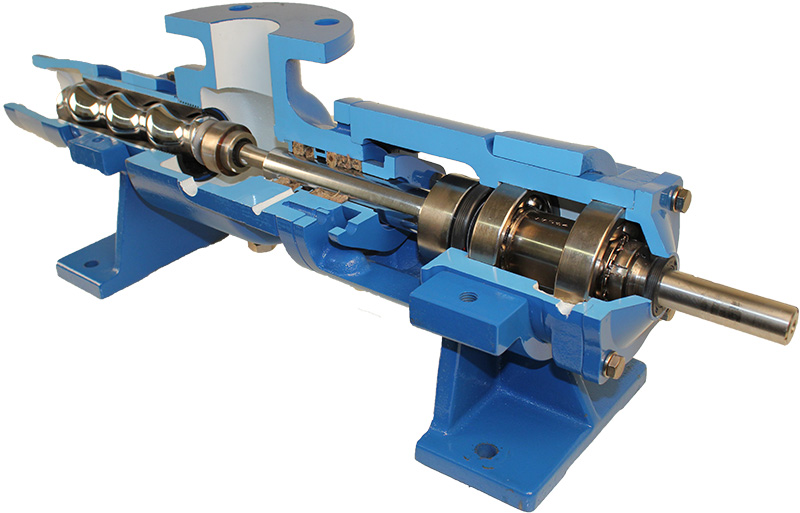
Screw pumps are commonly used in a variety of applications, including:
-
- Transferring viscous fluids: Screw pumps are well-suited for pumping high-viscosity fluids such as oils, molasses, and lubricants.
-
- Handling abrasive materials: The simple design of screw pumps makes them resistant to wear from abrasive particles in the fluid.
-
- Maintaining consistent flow: The positive displacement action of screw pumps allows for a steady, consistent flow rate, even as the fluid viscosity or system pressure changes.
-
- Gentle fluid handling: The low-shear action of screw pumps helps to preserve the integrity of delicate or shear-sensitive fluids.
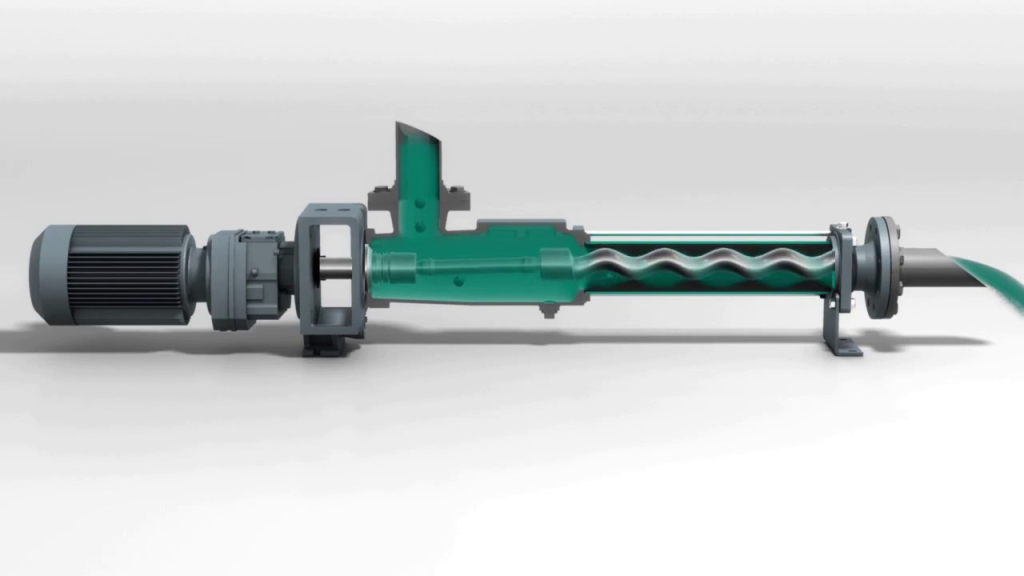
Screw pumps are known for their high efficiency, reliability, and ability to handle a wide range of fluid types and viscosities. They are commonly found in industries such as oil and gas, food and beverage, and chemical processing.