Screw Type Pump
What is a screw type pump?
A screw pump is a positive-displacement pump that uses one or several screws to move fluid solids or liquids along the screw(s) axis.
How does a screw type pump work?
The screw type pumps, as the name implies, the form of the screw is similar to a screw thread and hence by rotating it, the fluid moves along the screw thread from the suction side to the discharge side of the pump. Due to very close clearances inside the pump, the volumetric efficiency is high especially with viscous fluids as this reduces the amount of slippage of the fluid from the high pressure to the low pressure side. The pump itself like any positive displacement pump does not produce pressure, it only moves fluid but it is the actual system that produces back pressure due to friction loss.screw pump uses
What are the parts of a screw pump?
A screw type pump is made up of various components such as; a casing, a screw (depending on the types of screw pumps; it can contain 1 screw up to 5 screws),
bearings, a seal, a motor adapter and a drive shaft. Screw pumps are quite simple in construction.screw pump types
Single Screw Pump Diagram
The single screw pump diagram shows a pump that uses a single rotating screw to move fluid through a stationary cavity. The screw rotates within the stator, drawing fluid in at the inlet and forcing it out at the outlet. Single screw pumps are used in industries such as oil and gas, food and beverage, chemical processing, and wastewater treatment. They are capable of handling high viscosity, abrasive, and chemically aggressive fluids with low pulsation and shear.
What is the working of screw pump?
A screw pump works by using one or more screws or rotors to move fluid through the pump. As the screws rotate, fluid is drawn into the cavity and moves axially along the screw thread to the discharge end of the pump. The rotating motion of the screws also creates a progressive seal between the screw and the pump casing, which prevents backflow of the fluid. Its design allows it to handle viscous fluids with ease, making it a popular choice in various industries.
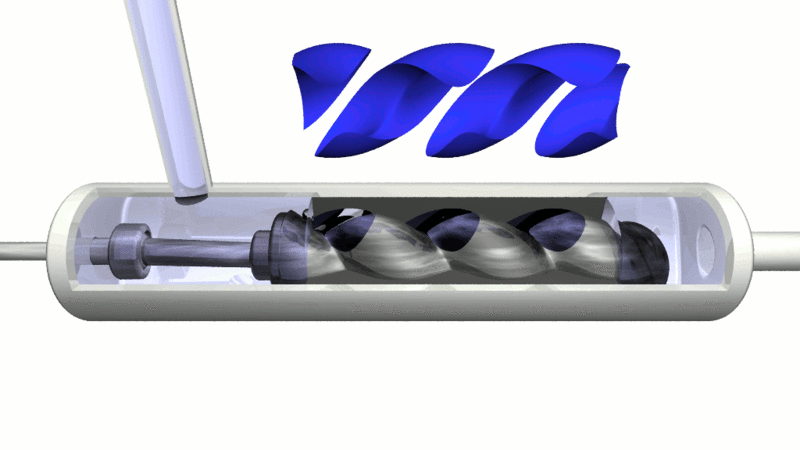
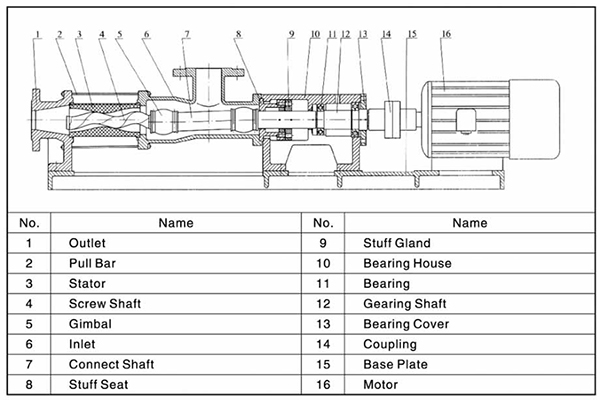
Screw Pumps Application
Screw pumps have become the standard solution for almost all industrial vacuum processes. Vacuum furnaces for brazing or sintering, metallurgical systems, and even steel-degassing equipment have the advantage of dust-proofing and long service intervals. In food processing, food drying, food packaging and even freeze dryers tend to use oil-free progressive cavity pumps to avoid contamination of the pump oil with water or process debris. Large-scale coating like architectural glass coating machine use a screw pump as a high vacuum pump rough pumping. Screw pumps are also ideal for the regeneration of large cryogenic pumps.
Many lubrication and hydraulic machines use screw pumps to supply oil for large machines.
Screw pumps are more helpful in pumping heavy oil. They even have the ability to pump higher flow rates and higher viscosity fluids.
These pumps are capable of pumping both liquids and gases. For this reason, these pumps are used in many pumping industries.
The pumps are also used in oil and gas, mining and manufacturing industries.
These pumps are used in the ceramic, chemical, paint, food and paper industries.
Advantages
- Characteristics of screw pump
- These pumps are easy to maintain.
- Progressive cavity pumps can be used for all fluid
- It can be dried up
- It has a compact structure
- These pumps provide constant and non-pulsating fluid flow
- These have a quiet operation
- The pump can produce greater volumetric efficiency
- High reliability
- Self-priming capability
- High robustness
- The progressive cavity pump does not pump contaminants in the fluid
- It has frictionless rotation
- With a progressive cavity pump, you can also pump high viscosity fluids without losing flow
- High resistance to water vapor and particles/dust
- Very high pumping speed
- No contamination of the pumped medium
- Frictionless rotation – eliminates rotor wear
- High efficiency due to internal compression
- Relatively low operating costs and maintenance requirements
- Inverter operation – easily optimized for process requirements – resulting in high energy efficiency
Disadvantages
- Installation costs for small industries are high.
- The pump requires gas ballast to transfer light gases quality
- Without gas ballast, the ultimate pressure and pumping speed of light gases (helium and hydrogen) are reduced
- cannot be scaled down to small pumping speeds below 50 m³/h; below approx. 100 m³/h multi-stage Roots or scroll pumps are used
Screw Pump Operation
Screw pumps are positive displacement pumps that move fluid by trapping it between the rotating threads of two screws or rotors. As the screws rotate, they create a continuous flow of fluid through the pump.
The operation of a screw pump can be broken down into three main stages: suction, compression, and discharge. During the suction stage, the screws rotate and create a vacuum that draws fluid into the pump inlet. As the fluid fills the voids between the screws, it is carried towards the compressed zone.
In the compression stage, the screws mesh together and compress the fluid between them. This action raises the pressure and moves the fluid towards the discharge outlet.
Finally, during the discharge stage, the compressed fluid is forced out of the pump through the discharge outlet as the screws continue to rotate.
Screw pumps are known for their ability to handle high-viscosity fluids with minimal pulsation, making them ideal for applications such as pumping crude oil, lubricants, and food products like chocolate or peanut butter.parts of screw pump.pumping screw
Welcome to PMV screw pump components for the screw pumps procurement.2-screw pumps
What is a screw pump?
Screw pump is a part of the dry compressed gas transfer pump series. They are positive displacement pumps that use one or more screws to move fluid or water along the screw shaft. These screws interlock to pressurize the fluid and move it into the system. These screws engage each other and reciprocate in the cavity of the cylinder. They are often used in industrial vacuum applications, often in combination with Roots blowers, and as oil-free roughing pumps in high vacuum and ultra-high vacuum systems. Please check out the description of various pumps.
What is the purpose of a screw pump?
Netzsch screw pump is mostly used on fluids of a higher viscosity, moving these fluids with screw pumps results in energy efficient and a relatively compact machine when compared to other pump types i.e centrifugal pump.
What is difference between gear pump and screw pump?
The operation of a screw pump is much softer with less pulsations, less noise and fewer vibrations, meaning longer lifespan. Gear pumps are noisier, more turbulent and cause more vibrations for the pump and pipework to withstand causing a lower working life.
What is the efficiency of a screw pump?
Archimedean screw pumps are capable of pumping heavily contaminated surface water or sewage, and even sand if they are specially designed for this purpose. The head is purely geodetic and ranges up to 6 m at efficiencies between 60 and 80 %.